Unrivaled energy efficiency pays off
ENRX’s Weldac tube and pipe welders continue to sell like hotcakes, and with good reason, according to Section Manager, Morten Lavergren.
“We can barely keep up with demand”, says Morten Lavergren, Section Manager for in-line systems at ENRX. “Just very recently we’ve sold six welders to a client in South America and 16 to a major European producer. We have also just sold our first Silicon Carbide (SIC) Weldac in China and have good contracts in Australia.”
So, what is the reason for the worldwide success of the Weldac tube and pipe welders?
“Well, it’s not just one thing”, Morten says. “But, without a doubt, the unique Weldac efficiency plays a big role. Our design has proven to work extremely well for use in our high-frequency welders, and we are industry leading as far as technology and electrical efficiency goes.”
With the new and more efficient SiC transistors in the high-frequency inverter power modules, welding output has been significantly boosted. SiC inverter technology gives an impressive efficiency above 91% average – 7% more than previous systems and a whopping 35% more than vacuum tube converters.
The design of the Weldac with SiC inverter modules always indicates the total efficiency from the mains supply to the welding coil terminal. For specific standard setups, the efficiency has been measured to be even above 95 %.
“In fact, during the testing of the transistors, the inverter efficiency was measured at 99,3 % at full output current,” Morten says.
Along with a constant high electrical power factor – 95% at all power levels – there are substantial cost savings to be had. Particularly these days, with power prices soaring to previously unheard-of heights.
“Definitely!”, Morten agrees. “The modest extra cost of a Weldac very quickly pays off with the much lower costs during operation.”
Obviously, cost cutting is not the only benefit. There are also considerable sustainability factors to be reckoned with: High efficiency, reduced material usage, improved output power and lower cooling water requirements all make Weldac the obvious choice for companies that wish to lower their environmental impact whilst making a healthy profit at the same time.
In addition to the welders, ENRX is also selling more pre-heating equipment – often to the same customers.
“Painting of pipes after production is something that’s becoming more and more popular”, Morten says. “So, the producers need a pre-heater in their production lines. We have a comprehensive range of solutions for this as well – with all the same benefits.”
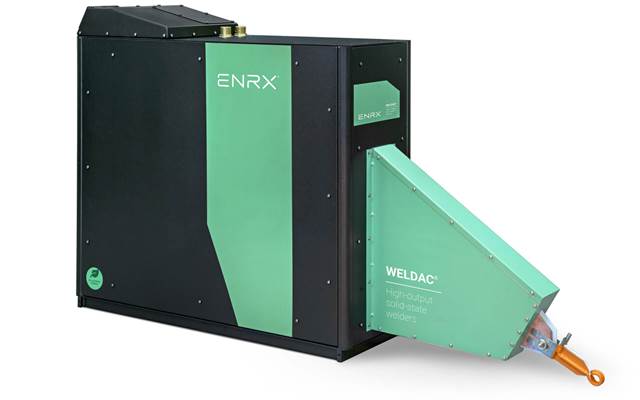
Weldac tube and pipe welders come in a wide range of power sizes.