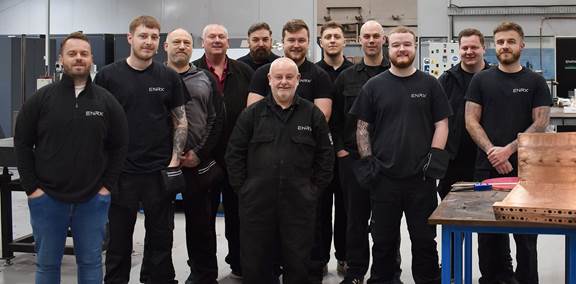
The coil connoisseurs
When it comes to induction heating, the coil is at the heart of the process. It’s the component that transfers energy efficiently, ensuring precise and consistent heating. At ENRX UK, coil manufacturing is more than just a service; it’s a craft perfected by a team with over 130 years of combined experience.
“Our goal is to ensure every customer gets the right coil, every time,” says Shaun Dangerfield, Head of Coils & Inductors at ENRX UK. “Whether it’s repeat orders, repairs, refurbishments, or brand-new designs, we have the expertise and technology to deliver.”
With a production facility and CNC machine shop in the West Midlands, ENRX UK provides high-quality manufacturing and repair services with dimensional repeatability. Using jigs, fixtures, formers, and CNC-machined parts, the team ensures precision in every coil they produce. For customers with ageing equipment and no existing drawings, ENRX UK can reverse-engineer older coils, creating accurate manufacturing plans to keep production lines running smoothly.
One of the company’s most innovative advancements is the development of pure copper printed heads. “For applications requiring absolute precision, we can design and 3D print working heads with engineered internal water flow—completely free of brazed joints in high-temperature areas,” explains Shaun. “This eliminates weak points and extends the lifespan of the coil by up to 60%.”
Beyond manufacturing, ENRX UK is a trusted partner for coil maintenance and refurbishment. The team offers full strip-downs of old coils, followed by acid cleaning, pressure testing, and the replacement of copper parts where necessary. Worn thermal components are redrawn and replaced, with new ceramic liners provided to extend durability.
For customers working with delicate heating applications, ENRX UK’s use of thermal imaging and advanced heating control makes a crucial difference. “Take aluminium brazing, for example,” Shaun notes. “When the base material’s melting point is dangerously close to that of the brazing filler, having real-time thermal monitoring ensures absolute precision and prevents costly errors.”
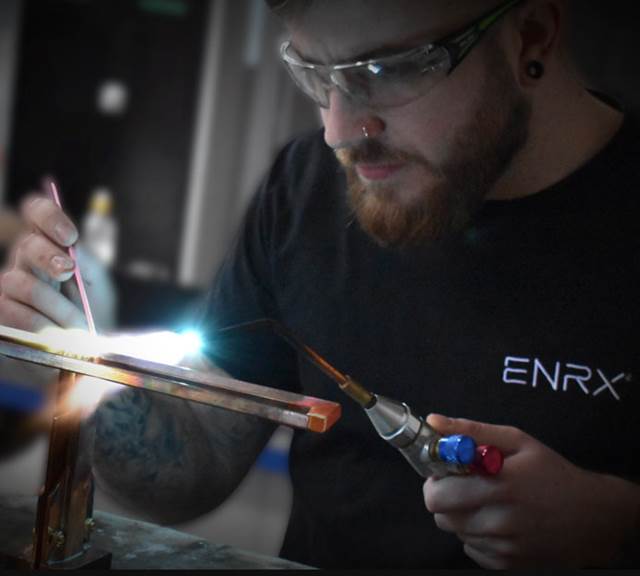
At the ENRX site in the West Midlands, they have a research & development department that are ready to take your call to discuss your coil needs.
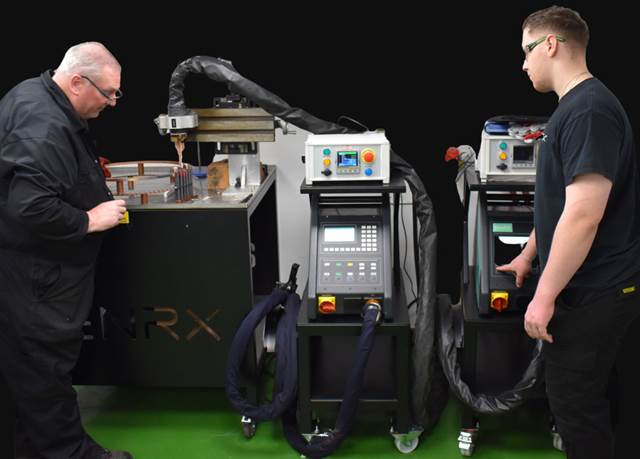
ENRX UK offers induction brazing training days for up to four people at one time.
The company also invests heavily in training and research. Their induction brazing training courses, tailored for up to four people at a time, help businesses optimise their processes. Additionally, ENRX UK’s research and development department is always ready to assist with feasibility tests, trial work, and application-specific research.
“We don’t just supply coils—we guide our customers through the entire heat treatment process, from initial design to final production,” Shaun adds. “For those seeking expert advice and top-tier coil manufacturing, ENRX UK is the go-to destination. Whether it’s a new design, refurbishment, or process optimisation.”
Shaun and his team ensure that every customer receives a tailored solution, keeping their induction heating operations at peak efficiency.
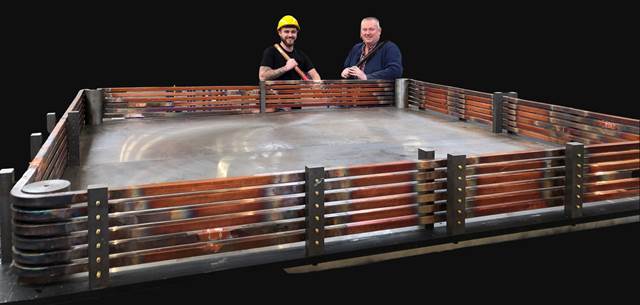
Coils can come in all shapes and sizes.
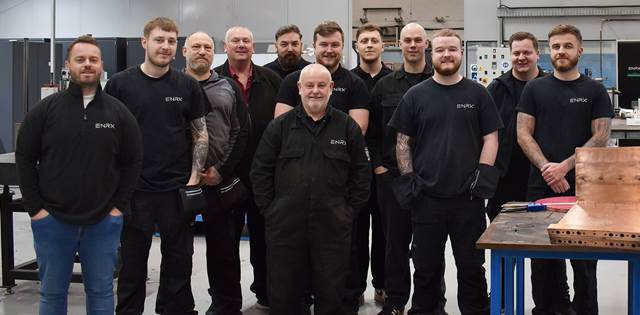
The coil team at ENRX UK with over 130 years of combined experience.