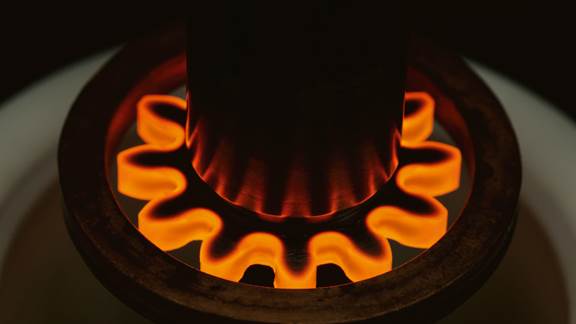
Induction heating - an introduction
Induction heating is a flame-free, fast, clean, energy-efficient, and non-polluting form of heating that can be used to heat metals or change the properties of conductive material.
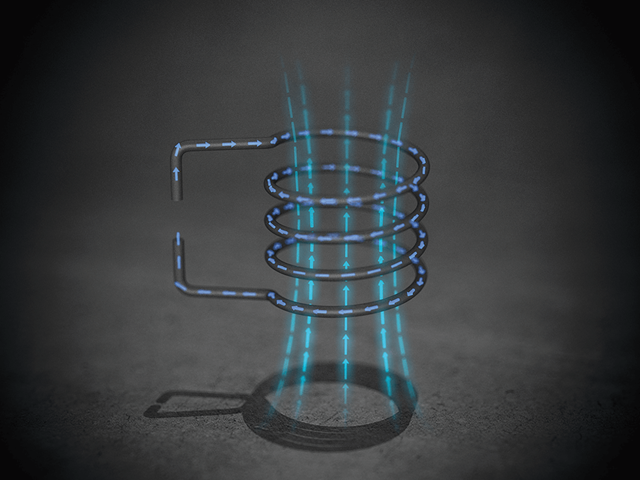
This is how induction heating works
Alternating current flowing through a coil generates a magnetic field. The strength of the field varies in relation to the strength of the current passing through the coil. The field is concentrated in the area enclosed by the coil; while its magnitude depends on the strength of the current and the number of turns in the coil.
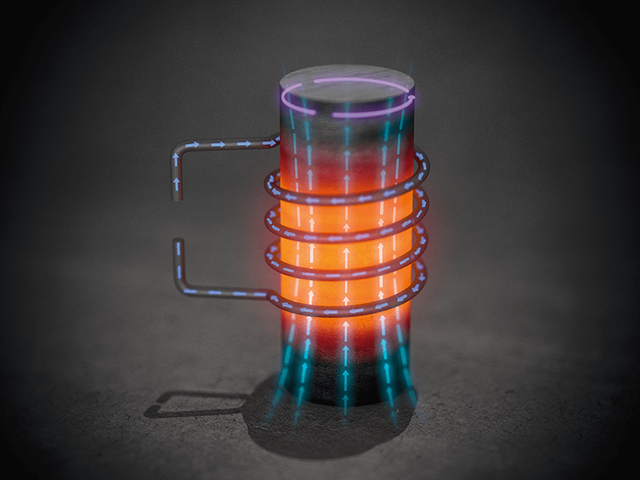
Eddy currents are induced in any electrically conductive object—a metal bar, for example—placed inside the coil. The phenomenon of resistance generates heat in the area where the eddy currents are flowing. Increasing the strength of the magnetic field increases the heating effect. However, the total heating effect is also influenced by the magnetic properties of the object and the distance between it and the coil.
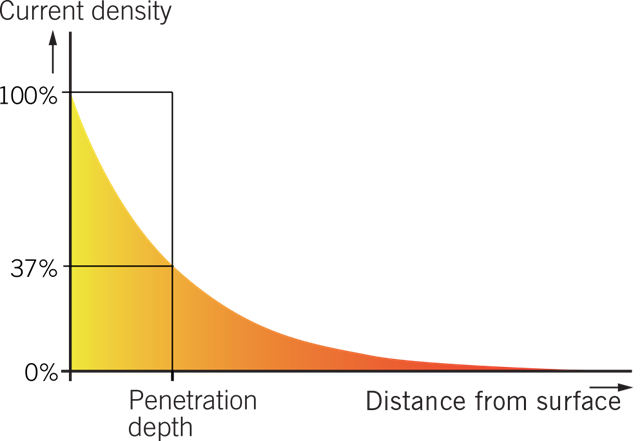
The eddy currents create their own magnetic field that opposes the original field produced by the coil. This opposition prevents the original field from immediately penetrating to the center of the object enclosed by the coil. The eddy currents are most active close to the surface of the object being heated, but weaken considerably in strength towards the center.
The distance from the surface of the heated object to the depth where current density drops to 37% is the penetration depth. This depth increases in correlation to decreases in frequency. It is therefore essential to select the correct frequency in order to achieve the desired penetration depth.
What are the benefits of induction heating?
The advantages over alternative technologies like an open flame or radiation are plenty.
Induction heating is:
- Faster. The produced heat in induction heating is instant. It takes less than one second to achieve a uniform surface temperature of 1,000°C on small metal components.
- More accurate. Just the right temperature is delivered, just where it’s needed to individual workpieces. And because of the range of frequencies available, to just the right depth. Heat distribution is precise, too. We can customize induction coils to suit practically any shape or size of workpiece. Customized coils ensure optimal heat patterns with minimum energy consumption.
- More controllable. Transistorized converters and process control software give you complete control over the entire heating process. Ramp-up and dwell times can be pre-set and repeated as often as you want. Equipment can also feature in-built telemetry devices for remote diagnostics and off-site monitoring.
- Repeatable. Induction heating lets you accurately repeat your desired heating cycle. (In fact, the produced heat from a frequency converter normally varies as little as 1-2%.) You can duplicate all the key parameters: temperature, penetration depth, heat pattern, speed-of-temperature increase, etc.
- Cleaner, safer, and more compact. No gas. No open flames. No noticeable increase in ambient temperature. No excessive floor space occupied by ovens. All this makes induction heating superior to other alternatives, and, not to mention, more sustainable as well.
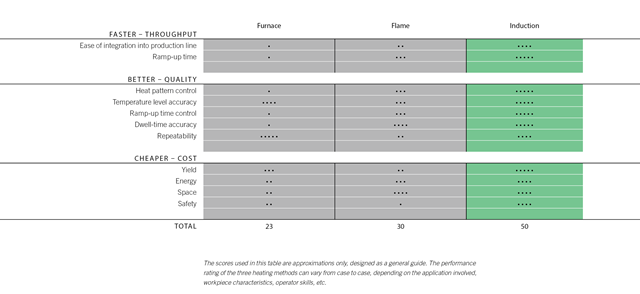
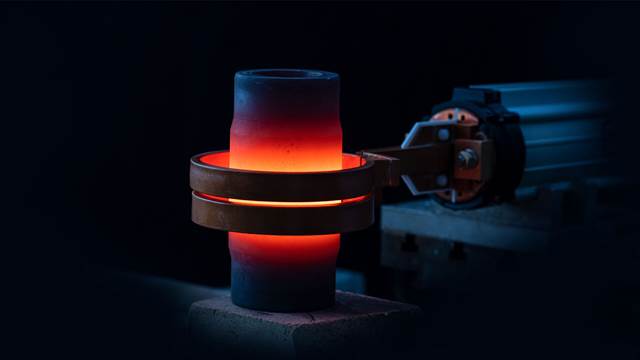
Faster. Better. Cheaper.
The technical features of induction heating deliver three key benefits:
-
Improved throughput
-
Better and consistent quality
-
Reduced costs
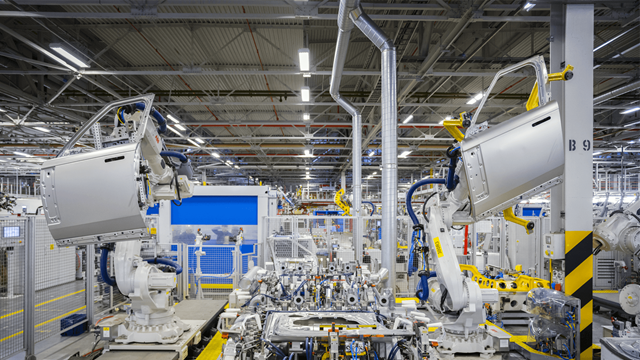
Improved throughput
Integrating induction heating into the production line improves production efficiency. You cut lead times and speed up throughput. The heating process itself is faster than with open-flame and oven alternatives. Accurate repeatability means you get to be faster because you get it right the first time.

Better and consistent quality
Quality improves because you can apply pre-set temperatures to pre-set parts of individual workpieces. And, because induction coils are tailor-made for specific workpieces, you know, in advance, the delivered heat pattern. Also, precise heat delivery means any adjoining components and materials remain unharmed during the heating process.
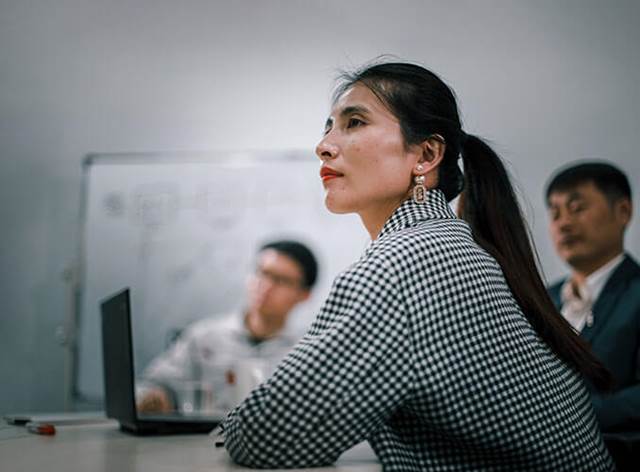
Reduced costs
Costs go down because of shorter lead times and increased throughput. Integrated in-line induction heating means lower administration and logistics costs. Production yields go up. Swift heat cycles, precise delivery and accurate repeatability minimize waste and scrap. Energy costs go down because you heat only what you need to heat—there are no costly heat losses as with conventional ovens. (ENRX frequency converters are particularly effective at lowering energy costs, as they have a proven higher efficiency and power factor than competing converters.) And, because induction heating lets you abandon hazardous gas and open flames, you can negotiate lower insurance premiums.
Induction technology for the widest range of applications
Induction heating is used in numerous industries worldwide. The technology of induction heating touches nearly all aspects of modern life.
A can of peaches, a cruise liner’s hull, a tub of yogurt, power station turbines, cables under the ground, pipelines under the waves, and countless trains, planes, and automobiles. What unites these different products is that induction heating is used to make them, maintain them, repair them, and recycle them. (In case the yogurt tub intrigues you, induction heating attaches the foil lid to the plastic container. As for canned peaches, induction heating helps coat the tin on the can’s inside so that conserved foods remain untainted.)
Every day, across every continent, induction heating is used to improve our lives. Just take the manufacture of an average family car for example. Induction is used for hardening camshafts, crankshafts, gears and steering parts. It bonds doors, boots and bonnets and joins the pipes in the air-conditioning system. Induction heating is used to make everything from faucets to spaceships. Simply put, induction heating solutions can be profitably used in virtually any industrial application that requires heat.
We think that's pretty amazing.
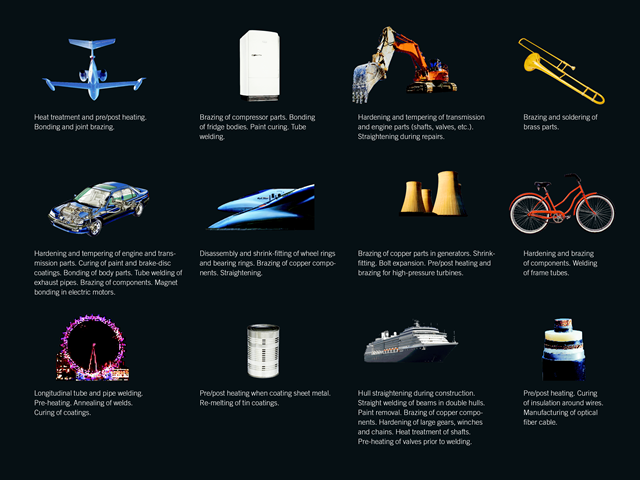
Selecting the best induction heating solution
Just how efficient is induction heating? What frequencies are best suited to your applications? The guide below will give you some idea of the potential of induction. To learn more, just contact your nearest ENRX office or representative.
How much energy do you need?
Before calculating your energy requirements you first need to know:
-
The type of material (steel, copper, brass, etc.)
-
Workpiece dimensions
-
Desired hourly production
-
Desired final temperature
Calculate your energy requirements
Step 1 First determine the material’s energy absorption rate. Fig. 1 shows rates for some common materials.
Step 2 Multiply the energy absorption rate by your desired hourly production (kg/hour). The result is your specific power requirement.
Step 3 You can now ascertain the overall efficiency level of the induction equipment. Some typical induction heater efficiency levels for common materials are listed in Fig. 2. Divide the calculated specific power need by the equipment efficiency rate. This gives you the total power requirement.
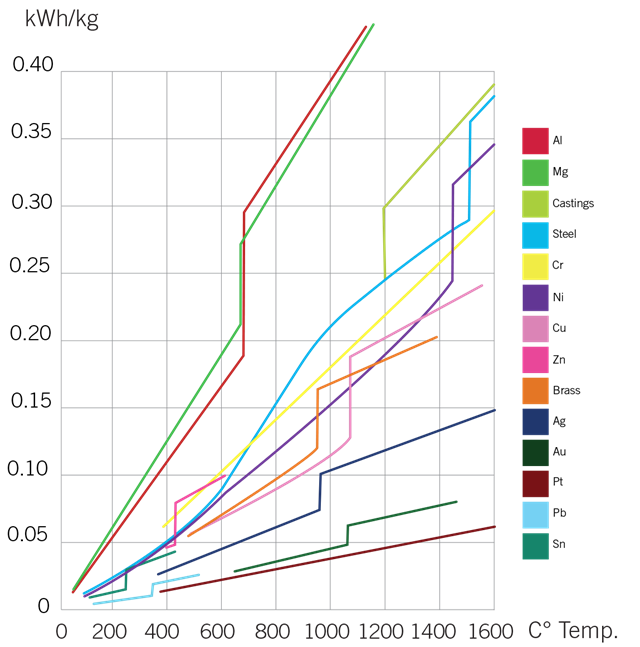
Fig 1. Energy absorption rate for different metals
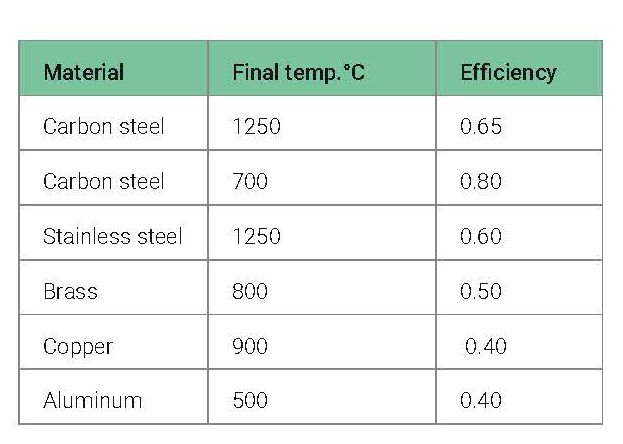
Fig. 2. Typical induction heater efficiency levels.The above values assume the use of enveloping multi-turn coils. Different coil designs may affect efficiency levels. For instance, the efficiency rate for copper is, because of the coil type normally used, usually 0.1-0.2.
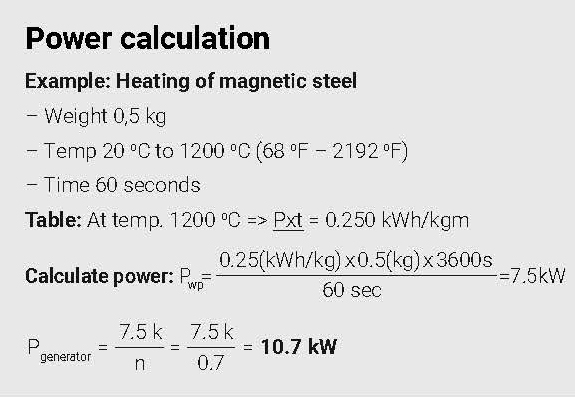
Power calculation
Example: Heating of magnetic steel
Selecting the right frequency
The choice of frequency is crucial when using induction heating, as frequency determines the heat’s penetration depth. Fig. 3 shows approximate frequencies for through-heating some common materials.
Fig. 3. Some economically beneficial ranges of dimensions for common materials at different frequencies. The frequencies shown are approximate guides only. The shortest heating time for specific materials and dimensions is achieved by operating close to the lowest possible frequency limit.
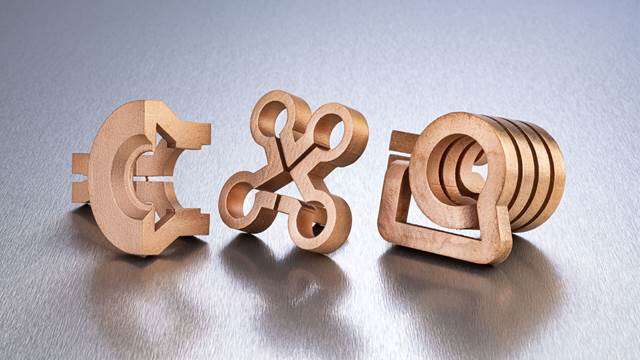
Quality is everyting
The induction coil, also known as an ‘inductor’, is essential to the induction heating process.
The induction coil. What it is.
The induction coil (also known as ‘inductor’, or ‘coil’), is one of the most important components in an induction heating system. It is also one of the most neglected and misunderstood.The problem is that too many people see the coil as little more than a copper tube through which cooling water and an alternating current are fed. But nothing could be further from the truth. In fact, a correctly designed and professionally made coil has a decisive impact in several areas.
Correct process outcomes
The heating patterns, temperatures and heat penetration depths achieved during an induction heating cycle are directly and profoundly influenced by the coil’s physical characteristics. A poorly designed or manufactured coil yields poor results.
Cost control
A professionally designed and manufactured coil that is properly maintained has a much longer and more productive working life than its amateurish counter parts. Also, a correctly built and maintained coil helps minimize waste.
Overall system efficiency
ENRX induction heating systems are designed to operate with ENRX coils. Using the correct coils means significant long-term savings.
A crash course in coils
Designing and making induction coils is not easy. Here are just three of the many challenges that need to be overcome in order to make safe, efficient coils.
Through-flow rate
It is critical to achieve adequate flow of cooling water through the coil. This is especially true with high-power density coils, as low through-flow results in insufficient thermal transference. A booster pump may also be needed to maintain the desired flow. Good designers specify a purity level for the water, in order to minimize corrosion on the inside of the coil.
Magnetic flux concentrators
Concentrators focus the current in the coil area facing the workpiece. Without them, much of the magnetic flux may propagate around the coil. This flux could engulf adjacent conductive components. But, when concentrated, the flux is restricted to precise areas of the workpiece. Concentrators are made from laminations, or from pure ferrites and ferrite- or iron-based powders. Each material has its own pros and cons.
- Laminations have the highest flux densities and magnetic permeability, and are less expensive than iron- and ferrite-based powders. Laminations are however stamped to a few standardized sizes and are therefore less flexible. They are also labour intensive to mount.
- Pure ferrites can provide outstanding magnetic permeability. But they suffer from low saturation flux density, and their brittleness makes them difficult to machine.
- Iron powders are easy to shape, offer high flux densities, and are easy to shape. However, care must be taken to protect against overheating, as internal losses or heat transfer from the heated workpiece mean such powders have a relatively low working temperature.
Impedance matching
It is necessary to achieve the correct impedance matching between the coil and the power source in order to use the latter’s full power. The designer must also consider that coils need five to ten times as much reactive as active power.
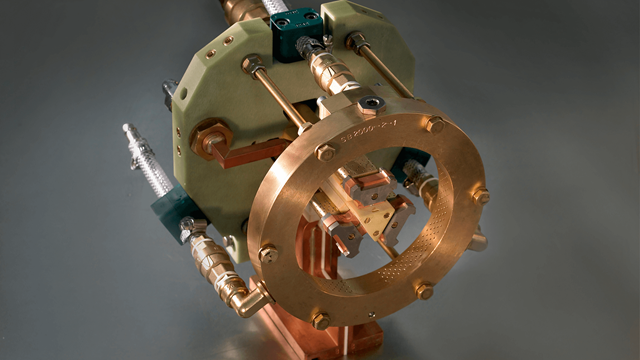
Customized induction coils
Single-turn, flexible, multi-turn cylindrical, left-turn, right-turn, rod-shaped, hair-pin, parallel, ear-shaped, new, reconditioned, tiny, big, unbelievably enormous. Conventional, machined, 3D printed or hybrid. At ENRX we design and make practically every type of coil imaginable.
Some amazing facts about induction heating
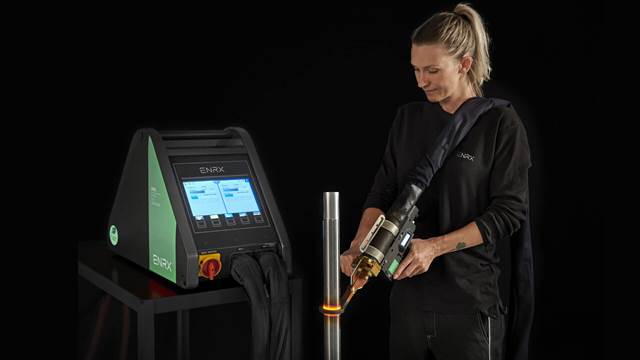
Using an ENRX mobile converter, you can heat 1 kg of steel from 20°C to 800°C in five seconds flat. That’s a speed-of-temperature increase of 160°C per second.
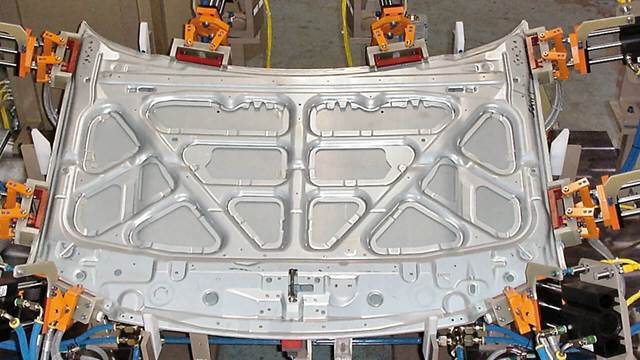
Induction heating is ten times more efficient than conventional ovens at curing the adhesives in automobile hoods. To cure one hood normally requires 220 kWs. As induction heating uses 340 kWs from the mains net, efficiency is 65%. Conventional ovens use something in the range of 4,000 kWs per hood, resulting in an efficiency of only 5.5%.
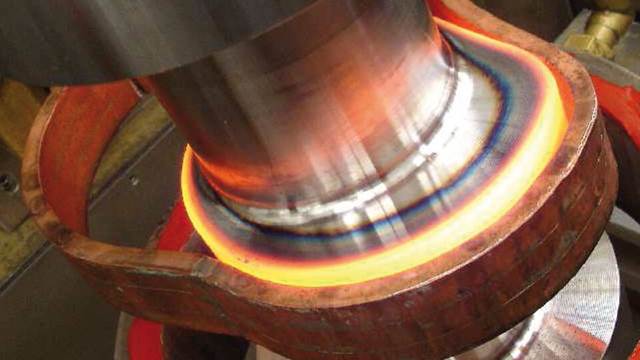
An ENRX frequency converter with an output power of 100 kW can harden a 60 mm diameter shaft to a depth of 2 mm (800°C at 2 mm) with a feeding speed of 1 m per minute.
Do you want to know more about induction?
Check out our articles below. They will give you a deep dive into the exiting world of induction and how it might benefit your industry and solutions.
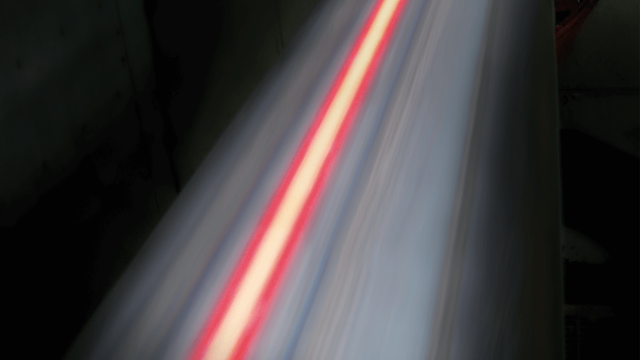
What is induction annealing?
Understand how induction annealing works and how it may benefit you.
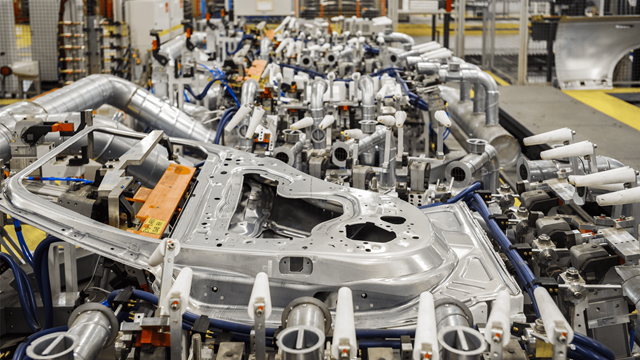
What is induction bonding?
Understand how induction bonding works and how it may benefit you.
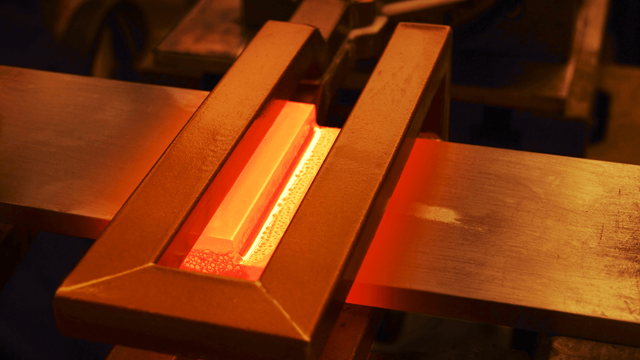
What is induction brazing?
Understand how induction brazing works and how it may benefit you.
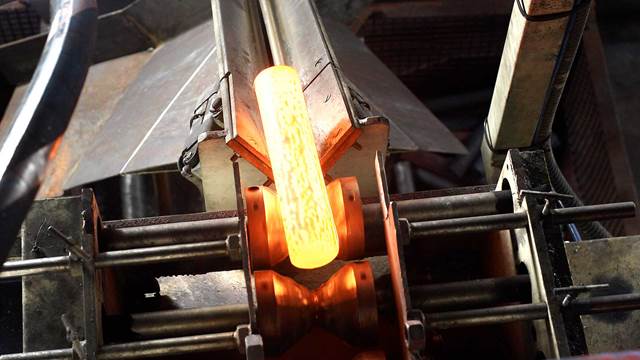
What is induction forging?
Understand how induction forging works and how it may benefit you.
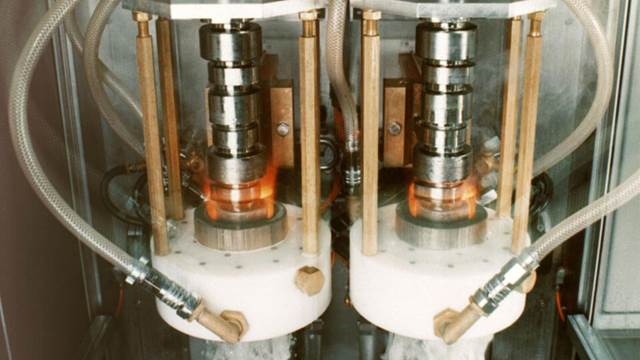
What is induction hardening?
Understand how induction `hardening works and how it may benefit you.
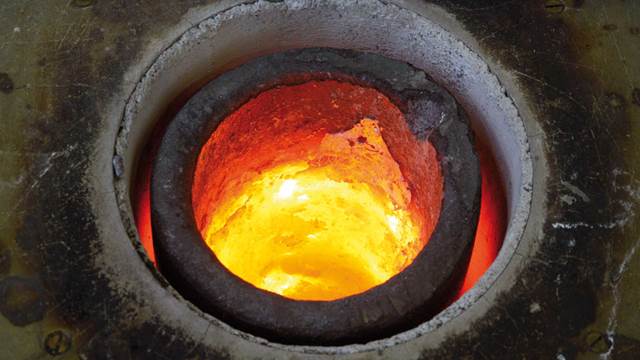
What is induction melting?
Understand how induction melting works and how it may benefit you.
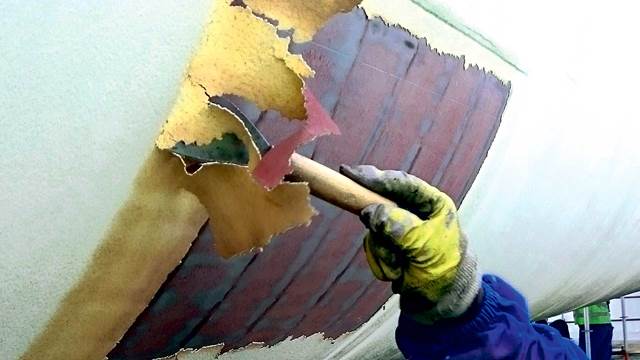
What is induction coating removal?
Understand how induction coating removal works and how it may benefit you.
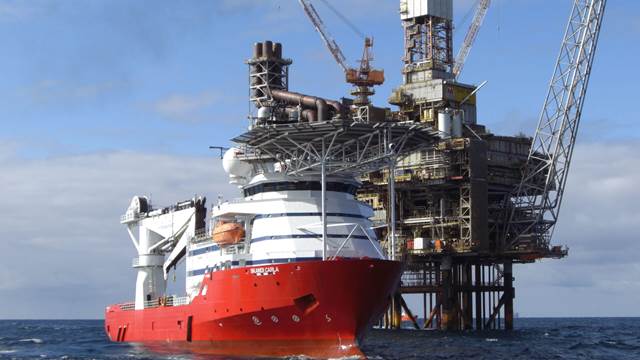
What is induction post-heating
Understand how induction brazing works and how it may benefit you.
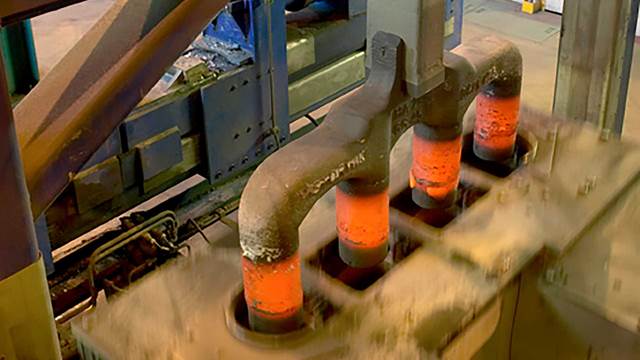
What is induction pre-heating?
Understand how induction pre-heating works and how it may benefit you.
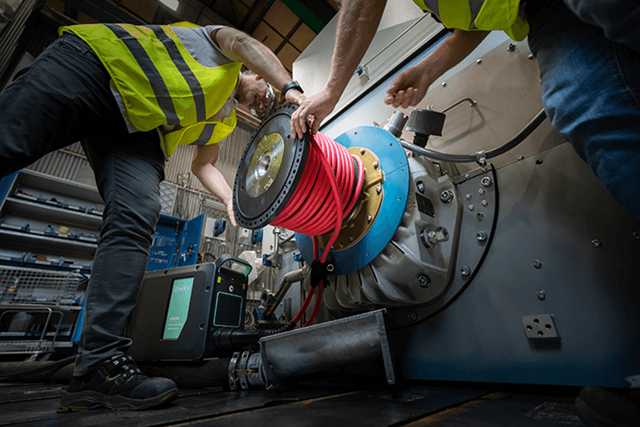
What is induction shrink-fitting?
Understand how induction brazing works and how it may benefit you.

What is induction straightening?
Understand how induction straightening works and how it may benefit you.
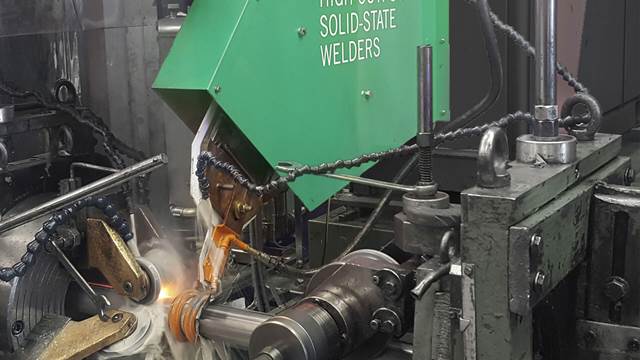
What is induction welding?
Understand how induction welding works and how it may benefit you.
Glossary
Lost in translation? We've gathered some of the terms when it comes to induction heating and give you a brief explanation.
Stainless steel is a common name for steel alloys that are resistive to corrosion and oxidation (rust). These normally include:
- Austenitic steel—the largest category of stainless steel, accounting for about 70% of all production. The austenitic class offers the most resistance to corrosion in the stainless group, due to its substantial nickel (Ni) content and higher levels of chromium (Cr). The steel is nonmagnetic and has no Curie point.
- Ferritic steel—the second-largest class of stainless steel, constituting approximately 25% of stainless production. Ferritic stainless steels are plain chromium (Cr) steels with no significant nickel (Ni) content; the lack of nickel results in lower corrosion resistance than the austenitic (chromium-nickel stainless steels). The steel is magnetic and has a Curie point.
- Martensitic steel—a small category of stainless steel characterized by the use of heat treatment for hardening and strengthening. Martensitic stainless steels are plain chromium (Cr) steels with no significant nickel (Ni) content. Th