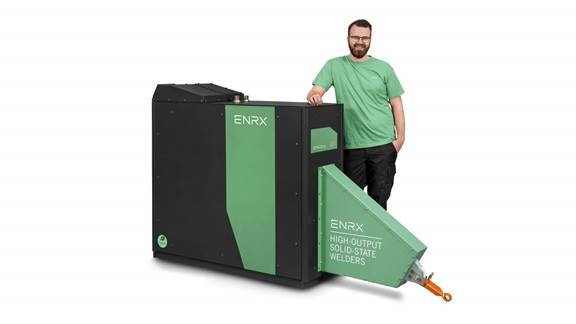
Takes industry by storm
Since its introduction in May of last year, ENRX’s new Compact Weldac high-frequency induction welder has made a huge impact in the tube and pipe industry. But, to what exactly does this welder owe its success?
The Compact Weldac hit the market like a storm last year. Despite the coronavirus-induced recession and low activity in global production, tube and pipe manufacturers lined up to buy.
“In fact, making them in batches of ten at a time is not enough to keep up with demand,” smiles Sales Manager Mark Prasek at ENRX USA, offering up his explanation of why this small Weldac has become so popular.
“To understand why the Compact Weldac took off like it did, we first need to understand the welder market”, he begins. “ENRX has long been a market leader in terms of technology, but better technology typically comes at a higher price. With larger welders, the high price of better technology can be more easily justified since they are used for larger product sizes on larger production lines that have very high downtime costs. In that case, technological advantages which benefit uptime, performance and energy savings become more important than equipment cost. It is the total cost of ownership that is paramount. On smaller welders running on smaller production lines, the technological advantages are more difficult to quantify.”
There are many low-cost welders on the market, so what ENRX aimed for was a welder that offered all the technological advantages they are known for, at a price point that could hold its own against low-cost competitors.
The solution came from using existing proven technologies coupled with advancements in silicon carbide (SiC) inverter technology and then packaging it into a new, more compact frame. A design that focuses on welders rated for 300 kW and below, as well as a design that can be used on the largest market segment of tube mills in the world.
“To be clear”, Mark points out, "the Compact Weldac is not a stripped-down or compromised design. It offers all the same benefits as its bigger brothers.”
Such benefits include a short-circuit proof design that protects the generator from arcs, flashovers, and direct shorts, resulting in higher uptime. The fully automatic electronic load matching means that no operator intervention is required. And, power regulation at inverter frequency is orders of magnitude faster than silicon-controlled rectifier (SCR) machines, so arcs and flashovers no longer need to be defects.
The Compact Weldac is industry leading as far as electrical efficiency goes, with 91% from the mains to the coil. Along with a constant high electrical power factor – 95% at all power levels – there are substantial energy cost savings to be had.
“The small footprint of the single-cabinet design not only makes the welder easy to install and retrofit, it requires less material to manufacture, so the lower consumption of both energy and resources makes the Compact Weldac a sustainable choice as well”, Mark says. “And last but not least, the advanced SiC inverter technology is covered by a 5-year warranty, which gives customers peace of mind.”
“So, the answer to the question of success is really very good foresight by all the various teams at ENRX”, he concludes. “Management, R&D, Engineering, Production and Sales all worked together to give the market what it wants.”Indeed, as a Sales Manager in North America, Mark has seen first-hand how the market has welcomed the Compact Weldac. Apparently, the first question many ask is: “Does it have automatic matching?”
“Unless you have experienced a poor matching situation, it’s difficult to explain the advantages of automatic load matching”, Mark says. “Some producers just learn to accept that their welder won’t deliver full power across the product mix. However, the Compact Weldac not only offers automatic load matching. As with all ENRX Weldacs, it runs continuous automatic electronic load matching, which is done without operator intervention or any internal moving parts. Customers tend to relax once they hear this.”
“The next surprise comes when looking at the installation requirements,” he continues. “The Compact Weldac is a single-cabinet machine, and that greatly simplifies installation, particularly in retrofit situations. Now, add a 5-year inverter module warranty and it becomes very clear this is not just like every other welder on the market. There are features with benefits at every point in the discussion”, he enthuses, brimming over with stories about how well the Compact Weldac has performed for customers.
“Recently, we won an order from a US tube producer who said: ‘With everything you’ve shown me, I don’t know why I wouldn’t buy an ENRX welder.’ I agreed, and they purchased three machines”, he smiles.
Another producer was experiencing increasing downtime from their existing welder. It was costing them considerable lost production at a time when they were already backlogged. Then they purchased a Compact Weldac. A month later, they came back for two more.
“A third producer was experiencing poor matching capability and increased downtime on their welder”, Mark recalls. “The Compact Weldac fit nicely on their existing positioning table. They actually started making tubes on the second day of commissioning and were using less power to weld the same tubes!”
“If ever there was a time to replace a vacuum tube or older solid-state welder, that time is now”, Mark Prasek believes. “The Compact Weldac will provide significantly reduced running costs combined with improved output power, raised efficiency, environmental benefits and better profit. Need I say more?”