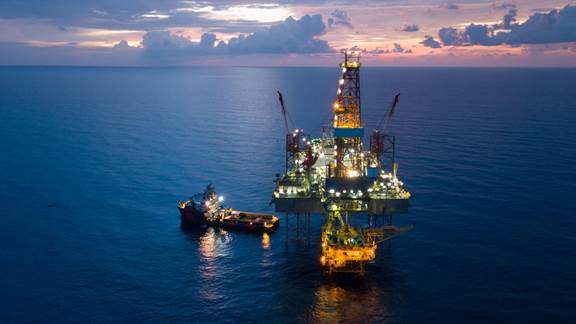
Pre- and post-heating
Induction heating is characterised by features that make it ideal for pre- and post-heating tasks: flameless, precise, mobile and versatile
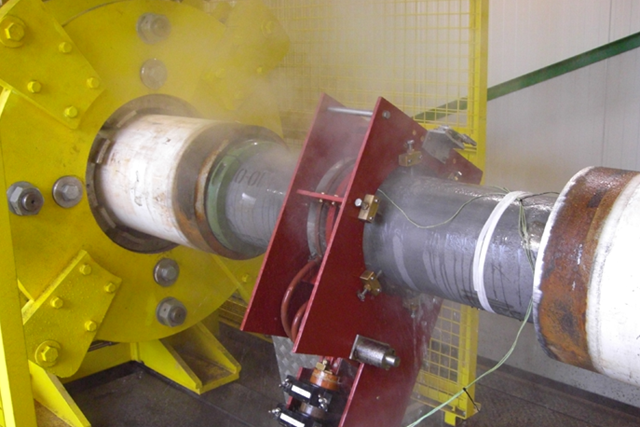
ENRX rental equipment and solutions are today used for applications such as:
- Pre-weld heat treatment
- Post-weld heat treatment
- Pre-heating before coating
- Pre-heating prior to cladding
- Pre- and postheating of swaged ends
- Pre-weld heating for subsea hot tapping
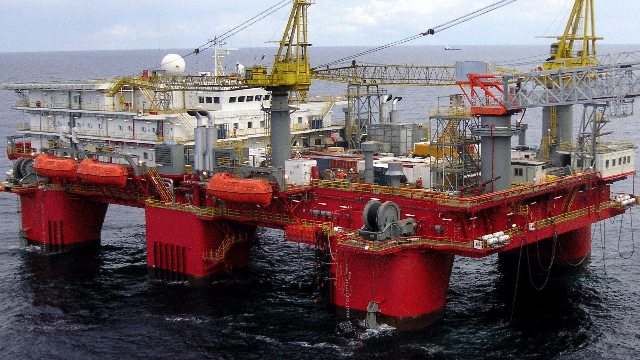
Platform-based case story
Mobile heating equipment from ENRX was used to help repair a steel bulkhead on the ‘Safe Concordia’ accommodation and support platform.
The equipment—an ENRX mobile Minac 25/40—pre-heated the weld area before and during the welding of a 40mm-thick steel patch onto one of the platform’s crane towers. To ensure optimal weld results, the weld area needed to be pre-heated to 80-100 °C, then maintained at that temperature throughout the entire welding process. Such weld pre-heating is often carried out using resistance heating pads or mats. But as Jon Philpott, the ENRX engineer who performed the pre-heating explains, the presence of highvoltage cables near the weld area ruled out resistance heating. “Induction is not only flame-free, it is also extremely fast and localized. This means induction heating results in minimal stray heating and
heat soak, especially when compared to resistance heating.”
The contractor chosen to weld the patch, Whittaker Engineering, tested the ENRX equipment at its base outside Aberdeen, Scotland. “The offshore industry has tough safety and quality standards,” says Ken Whittaker, Whittaker Engineering’s co-founder. “ENRX had to first prove their solution could do the job while satisfying these requirements. Once that was achieved, the equipment, together with an ENRX offshore engineer, set off for Curaçao in the Caribbean. I’m more than happy with the result, and with the cooperation between us and ENRX.”
The ‘Safe Concordia’ is a six-column, semi-submersible accommodation platform with capacity for up to 455 persons. The platform is owned by Prosafe, the world’s leading owner and operator of accommodation/service rigs. The company owns eleven semisubmersibles and one jack-up. Accommodation/service rigs have traditionally been used wherever there is a need for additional accommodation, engineering, construction or storage capacity offshore. Typically, these rigs will be employed for installing and commissioning new facilities, upgrading or maintaining existing installations, hooking-up satellite fields to existing infrastructure, and removing installations.
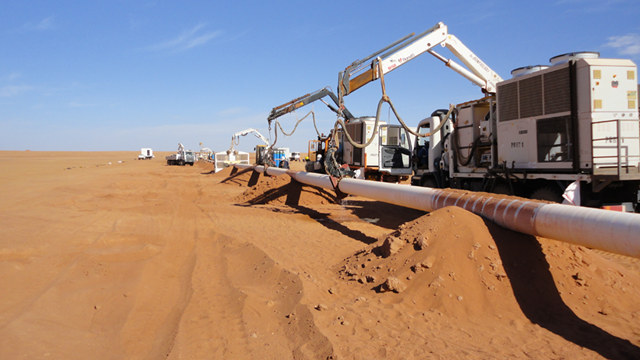
Land based case story
PWHT systems used for butt welding
The In Salah Gas (ISG) project is a joint venture between Statoil, BP and Sonatrach. The project is currently Algeria’s third largest gas development, with an annual production capacity of around 9 billion cubic meters. The latest phase of ISG—named the In Salah Southern Fields project (ISSF)—calls for the construction of the world’s longest 13% Cr onshore pipeline. Bonatti, the international pipeline construction specialists, were chosen to build the corrosion-resistant network of pipelines needed for ISSF. “This is a significant project for several reasons,” says Stefano Migliavacca of ENRX. “To be selected by such a prestigious company as Bonatti confirms our ability to satisfy the most stringent criteria. The project also underscores the industry wide acceptance of our PWHT solution for corrosion-resistant alloys.”
The Bonatti order involves two complete post-weld heat treatment (PWHT) systems for on-site operation in the Saharan desert. Each system is truck-mounted, and comprises an ENRX Minac 70/100 power source, specially designed induction coils for 8”-12” and 16” pipe, a chiller, and quench units. The two PWHT systems will be used for butt-to-butt welding of 13% Cr and of 13% Cr to duplex steel. “Welding these heterogeneous materials is a technically advanced task,” says Migliavacca. “But when used in conjunction with PWHT, such welding offers tremendous benefits. 13% Cr pipe, for example is extremely cost-effective because its strength means that lighter wall thicknesses can be used. Duplex on the other hand is extremely resistant to corrosion.”
PWHT of 13% CR and duplex flowlines is necessary in order to minimize the risk of hydrogen induced stress cracking. Such cracking is caused by the presence of hydrogen in the pipe’s heat affected zone. Although precautions are taken during the fabrication and welding stages to minimize hydrogen content, PWHT is still deemed the best way to achieve safe levels. “A big factor behind Bonatti’s decision is our proven experience in this specialized PWHT area,” adds Migliavacca. “Our colleagues at ENRX in the UK, Jon Philpott in particular, had previously devised a PWHT solution for another In Salah contractor. It involved the supply of three truck-mounted PWHT units, which have now been operating in the tough Algerian environment for months. Philpott’s expertise contributed greatly to the Bonatti solution, and helped convince them that ENRX was the right partner.”
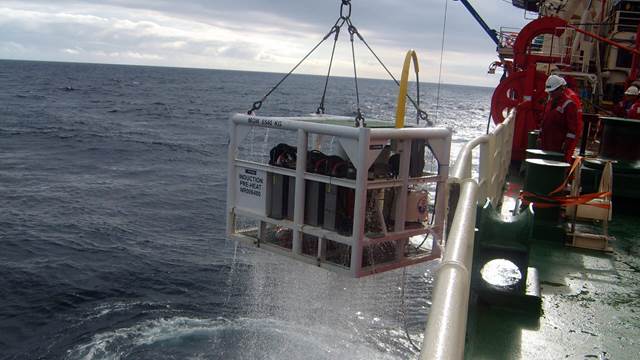
Subsea case story
ENRX played a key role in the Statoil Tampen Link project in the North Sea. The goal of the project—for which Technip Norway was the main contractor—was to connect the Statfjord field gas-export line with the Shell UK FLAGS (Far North Liquids and Associated Gas System) export pipeline.
The connection involved bringing a 12” branch pipe into a live, high-pressure 20” main gas line at a depth of 145 m (475’). Joining the two pipes—while still maintaining a high-pressure flow of gas in the main line—called for the use of ‘hot tapping’. Put simply, hot tapping involves welding a blind branch onto the main, live pipe. A ball valve is attached to the blind branch and a special hot tapping machine is then attached to the valve assembly. This machine is basically a large drill that cuts a hole through the main pipe. The cut-out metal (called a ‘coupon’) is retrieved, the valve closed and the drill removed.
Hot tapping is a challenging operation. One of the more serious problems facing engineers is a heat-sink effect caused by the high-pressure flow of gas inside the main pipe. Any heat introduced into the main pipe is immediately removed by this fast-flowing cooler gas. The heat-sink is especially problematic because the first step in hot tapping is the application of a ‘butter layer’ or ‘butter weld’ on the outside of the main pipe. The branch is welded onto the butter layer, which acts as a transitional zone giving desired metallurgical qualities. However, the application of the butter layer, as well as the subsequent welding, calls for pre-heating. And it is this preheating that is difficult to achieve because of the heat-sink effect.
The traditional way to pre-heat a live pipe in preparation for a butter layer is to wrap the pipe with heating mats. However, the large size of the main pipe in the Tampen project (20”) and the massive cooling effect caused by the flow of pressurized gas (approx. 150 bar / 2175 psi) ruled out the use of such mats, as the radiated heat would make working conditions intolerable for the welder divers. Induction heating, however, produces heat directly within the workpiece, in this case the surface of the pipe. Also, profiled induction coils ensure that heat is generated only in very precisely defined locations and to precise depths. These features mean that intense and controllable heat is induced in the pipe, but with only negligible increases in the ambient temperature.
Minimal diver operations
The induction pre-heating solution devised for the Tampen project involved three induction coils, two shaped to fit the main pipe, and one shaped to heat the branch pipe. The solution also included 16 thermocouples placed in the heating zones and weld areas. As a key objective of the system was to minimize the divers’ manual operations, most control functions were either automated or allocated to the topside team. Only the induction coils and the thermocouples were brought into the welding habitat.
The supply power on deck was standard ship voltage of 440 V at 60 Hz. This was stepped up to 1,200 V to minimize the size of the main umbilical. A subsea transformer stepped the voltage back down to 440 V at 60 Hz. The ENRX inverters then stepped the voltage above 700 V and increased the frequency to a very high kHz range. The cables to the coils terminated in compact hand-held transformers, which converted the voltage to below 28 V. This resulted in induction coils operating at low voltage but very high frequency. Perry Slingsby Systems Ltd. (PSSL) packaged the system for subsea operations, providing all the power, instrumentation, control and operations support.
Submerged for five days
The pre-heat and welding operations were extensively tested at the UK’s National Hyperbaric Centre in Aberdeen. These tests confirmed that induction had the precision and power to offset heat-sink effects in the weld areas. The testing also gave engineers a chance to assign a power trip alarm to each thermocouple—an important safeguard to prevent overheating and possible collapse of the main pipe. The alarms were then fitted with delays. This was in order to avoid false warnings being triggered whenever the welding stick passed a thermocouple, resulting in a momentary temperature spike.
The subsea phase of the operation was carried out from the CSO Wellservicer, a Technip diving support vessel. Technip also provided the subsea welding habitat. The pre-heating subseawork skid was supported by an umbilical reeler on the ship. A single container on the ship’s deck provided all the power and many of the controls needed for the entire pre-heating operation.
ENRX On Demand
Our rental equipement
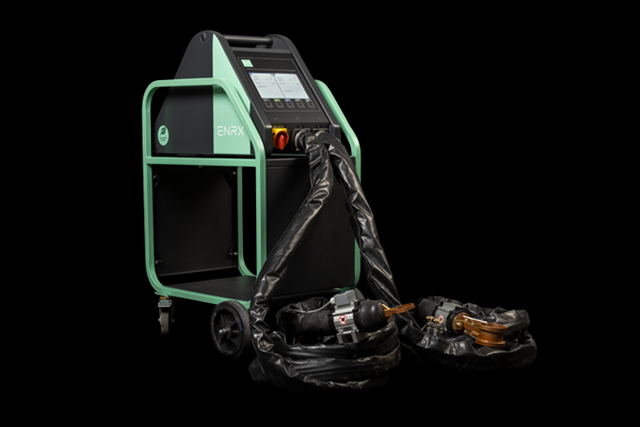
Minac
Minac is our family of mobile and versatile induction equipment. Examples of ideal jobs are brazing, curing, hardening, shrink-fitting and straightening. Minac equipment can be fitted with a single or twin output, various coils and coil fixtures, flexible cables, closed or separate cooling systems, and specially designed heating cables. We equip the Minac to fit your need.
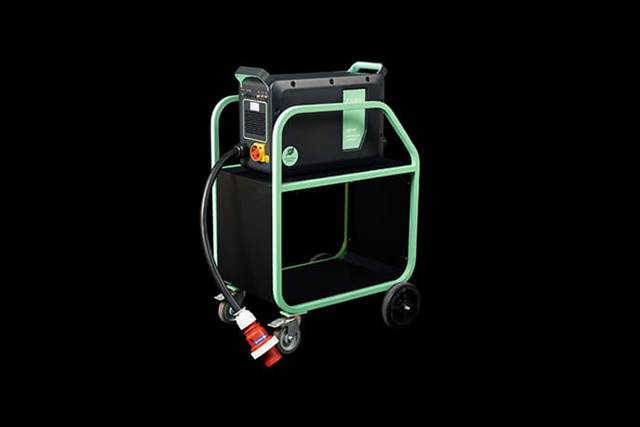
Ventac
Ventac is a portable air-cooled induction heating system that combines high continuous output (25 or 50 kW) with small size and low weight (only 36 kg). It has a sophisticated temperature control system that lets you stay in charge of your induction heating process. You get the task done quickly and can easily continue with the next one.